Hansastr. 32, 80686 Munich / October 09, 2025 - October 10, 2025, 9:30 am to 4:00 pm each day, further dates on request
EU AI Act and High-Risk AI Systems
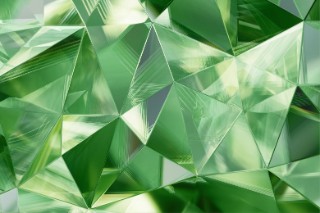
Fraunhofer IKS is organising a training course on the EU AI Act. Get an overview of the EU AI Act and its implications, dive deeper into the compliance approach and the verification methodology.
more info